How Motion Control - Brush & Brushless Direct Drive DC Motors can Save You Time, Stress, and Money.

115 VAC Brushless Motors - Groschopp
Not known Facts About Brushless DC Motors - RobotShop
When transforming electricity into mechanical power, brushless motors are more efficient than brushed motors primarily due to the absence of brushes, which reduces power loss due to friction. ARC Systems boosted performance is biggest in the no-load and low-load regions of the motor's performance curve. Environments and requirements in which manufacturers use brushless-type DC motors consist of maintenance-free operation, high speeds, and operation where sparking is harmful (i.


Advantages and Disadvantages of Brushed and Brushless Motors - A GalcoTV Tech Tip - YouTube
explosive environments) or might impact electronically sensitive devices. The construction of a brushless motor resembles a stepper motor, but the motors have crucial distinctions due to distinctions in implementation and operation. While stepper motors are regularly stopped with the rotor in a defined angular position, a brushless motor is generally planned to produce constant rotation.
Some Of Brushless Motors Selection Guide - Engineering360
Both a stepper motor and a properly designed brushless motor can hold finite torque at no RPM. Controller executions [edit] Since the controller carries out the standard brushes' functionality it needs to understand the rotor's orientation relative to the stator coils. This is automated in a brushed motor due to the repaired geometry of the rotor shaft and brushes.
Others measure the back-EMF in the undriven coils to infer the rotor position, getting rid of the need for different Hall impact sensors. These are therefore frequently called sensorless controllers. Controllers that sense rotor position based on back-EMF have extra obstacles in starting movement due to the fact that no back-EMF is produced when the rotor is fixed.
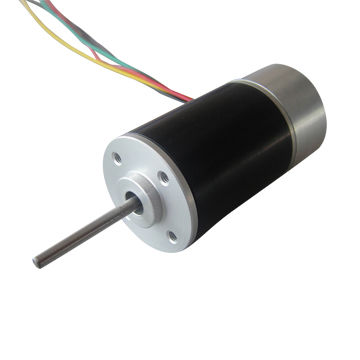
Brushed DC Motors VsBrushless DC Motors
Facts About Benefits of a Brushless DC motor Over a Brushed Motor Uncovered
This can trigger the motor to run backwards quickly, including a lot more intricacy to the start-up sequence. Other sensorless controllers are capable of measuring winding saturation triggered by the position of the magnets to infer the rotor position. [] A typical controller contains three polarity-reversible outputs controlled by a reasoning circuit.
Advanced controllers employ a microcontroller to handle velocity, control motor speed and fine-tune efficiency. Two key performance specifications of brushless DC motors are the motor constants K T \ displaystyle K _ T (torque constant) and K e \ displaystyle K _ e (back-EMF continuous, also called speed consistent K V = 1 K e \ displaystyle K _ V = 1 \ over K _ e ).